Electronic Batch Records Upgrade to PAS-X
October 18, 2018
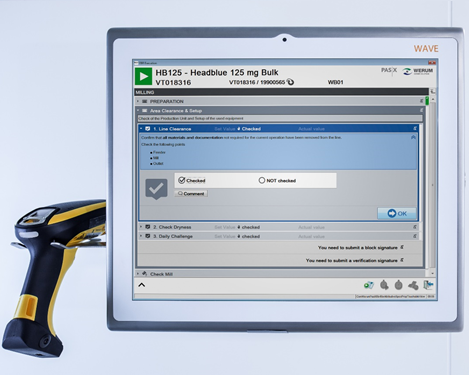
A pharmaceutical manufacturer recently engaged Grantek to upgrade their manufacturing control systems. This customer implemented Werum’s PAS-X software for generating electronic batch records (EBR). Part of Grantek’s role was to ensure that the required process information was supplied to the EBR system.
Existing System Overview
The previous system used a SCADA system with an Oracle database to store data. The SCADA system communicated with 13 different Programable Logic Controllers (PLC), not all of the same type. Recipes that defined phase parameters, sequencing, and phase entry/exit criteria were stored in the Oracle database. Recipe processing was handled by the vBatch component of iFIX.
Replacement System Overview
The new system replaced vBatch, iFix, the Oracle database, and the 13 PLCs with 3 ControlLogix PLCs. Two of the new PLCs control the process using existing converted code from the original 13 PLCs and the third PLC functions as the recipe controller/data concentrator. Alarms were moved to the data concentrator PLC and now use FactoryTalk View Alarms and Events to display and distribute alarm messages. The message data is stored on the data concentrator PLC and is triggered by monitoring the running recipes.
Grantek’s Role
Grantek’s role on this project was to upgrade the system feeding data to the PAS-X EBR software while ensuring data integrity was maintained. Grantek provided the skills and capability to define and build the manufacturing execution system (MES) to control system interface and feed data into the EBR system. It was the customer’s desire to keep the existing controlling phase logic to minimize downtime and validation testing. To accommodate this, Grantek designed and built a recipe processing system executing in the recipe processing PLC that emulated the vBatch interface to the phase logic. The Grantek designed MES-PLC interface is command based allowing for minimal configuration of the OPC Data server and allowed heavy re-use of MES designed components and routines.
As part of the project, Grantek developed a detailed system functional description outlining the data processing required at each step. The MES team handled operator interaction for processing of manual steps and storing of batch records and process deviations. Manual steps required interaction to the recipe processing PLC through the Grantek designed MES-PLC interface.
The upgrade was successful, validation effort was reduced, and data integrity of the EBR system was maintained. Grantek’s integration expertise enabled us to set up the new MES system correctly in order to provide accurate data to the plant’s EBR system.